Threading
Threading is an easy, well known and highly efficient manufacturing process. The process of cutting the threads in a hole is called “Threading” the hole. Admissible expertise combined with powerful R&D resources, place Mulph at the forefront of technical innovations in cutting tools. Our products cover application machine taps for through and blind holes in steel, stainless steel, high resistance steels, cast iron, super alloys and non-ferrous metal machining with high precision and thread quality.
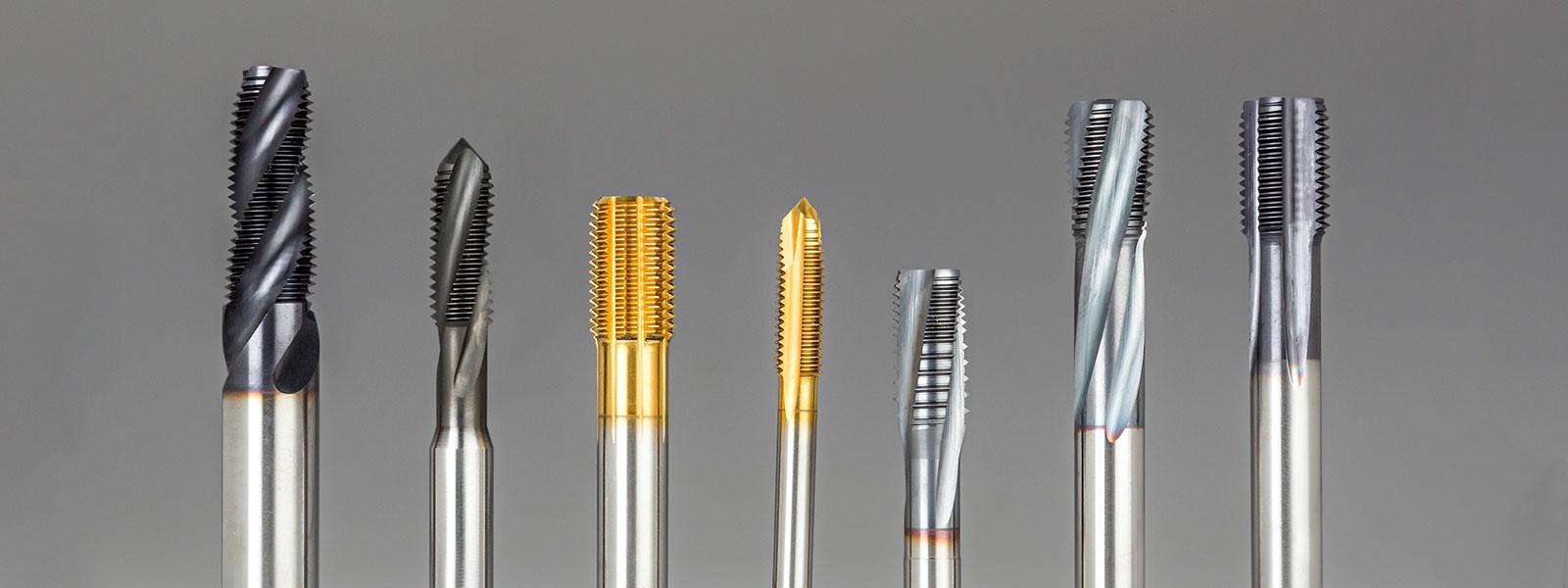
With using only high-quality premium material such as PM Cobalt, Cobalt HSS, HSS and carbide, MULPH threading tools are designed to perform at highest speeds, maximize tool life whilst producing high quality repeatable threads. Our Threading tools are produced based on both ANSI and DIN specifications for a variety of applications.
A conventional tap cuts a thread as opposed to forming the material. Cut taps are more popular than roll taps as they cover a wider range of materials, and also feature material specific geometries. For a Blind hole you would opt for a spiral flute, which brings the swarf out of the hole, whilst for a through hole you would opt for a spiral point tap.
FORMING TAPS with the coolant ejection channels for maximum performance. Short chamfer, no chip production, for through and blind holes. TIN-coated. For machining materials with good cold deformation characteristics and at least 10% elongation, for example: non-alloy steel up to 1000 N / mm², steel resistant to oxidation, acids and moisture, aluminum and its long chipping alloys.
What we offer is a massive range of taps for the creation of internal thread forms.